Students Help Develop Improved Radio Wave Process for Teradyne
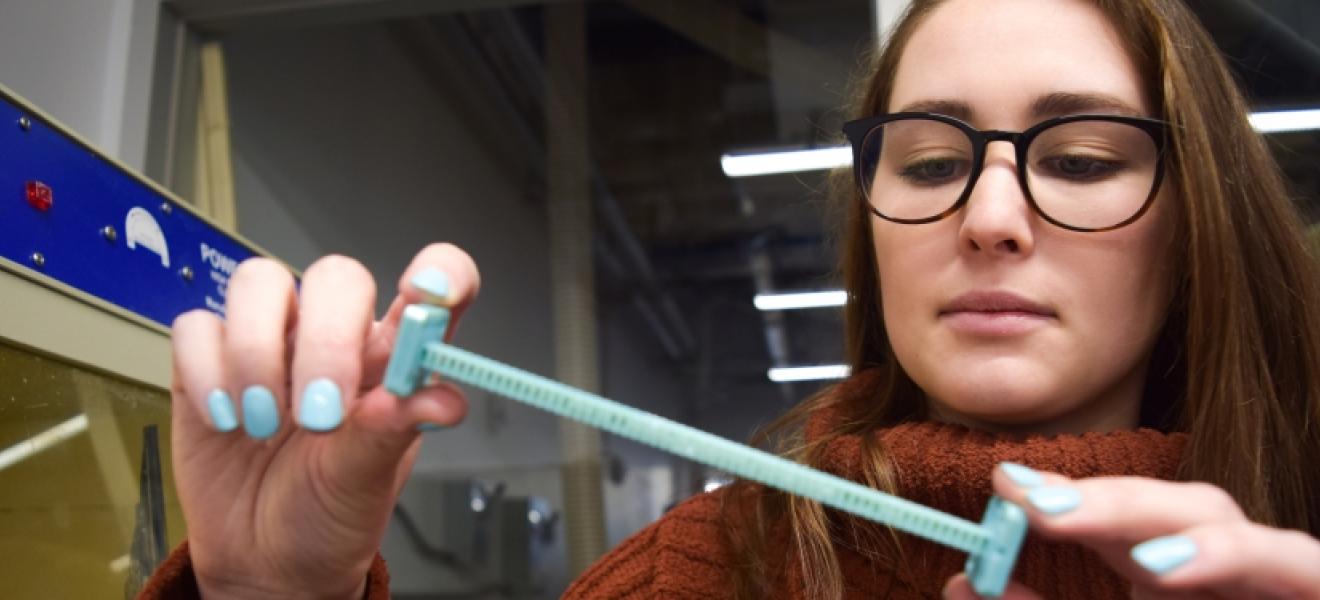
Tina Zunino works on the wave guide (Photos by Kristen Eckman)
While working with Teradyne Inc. as an engineering co-op, Wentworth Electromechanical Engineering student Abbie Petersen noticed the process in place for prototyping millimeter wave (mm-wave) components was inefficient. She decided to do something about it and Teradyne provided the grant to do it.
Electromagnetic radio waves that lie within the frequency range of 30–300 GHz are known as mm-waves and serve a variety of functions including airport security scanning, short-range wireless network connections, the development of 5G and scientific research. The typical prototyping process of extruding or machining mm-wave components is not only time consuming but also expensive and it lacks flexibility.
When Peterson heard electronic test and industrial automation company Teradyne was offering a grant to students with innovative ideas that could advance the company’s mission, she had a proposal. Peterson teamed with her fifth-year classmates Tina Zunino and Nick Piscitello to propose a senior design project and grant submission that sought to make it easier for engineers to identify the best prototyping methods for their own wave guide development using data collected by the team.
Teradyne selected the team’s grant proposal.
“Abbie listened to the problems around her, imagined ways to solve them with the skills she acquired at Wentworth, and pulled together a team and a solid presentation to sell it to our grant program management,” said mm-wave systems engineer Brian Wadell. “It was hard to say no to that!”
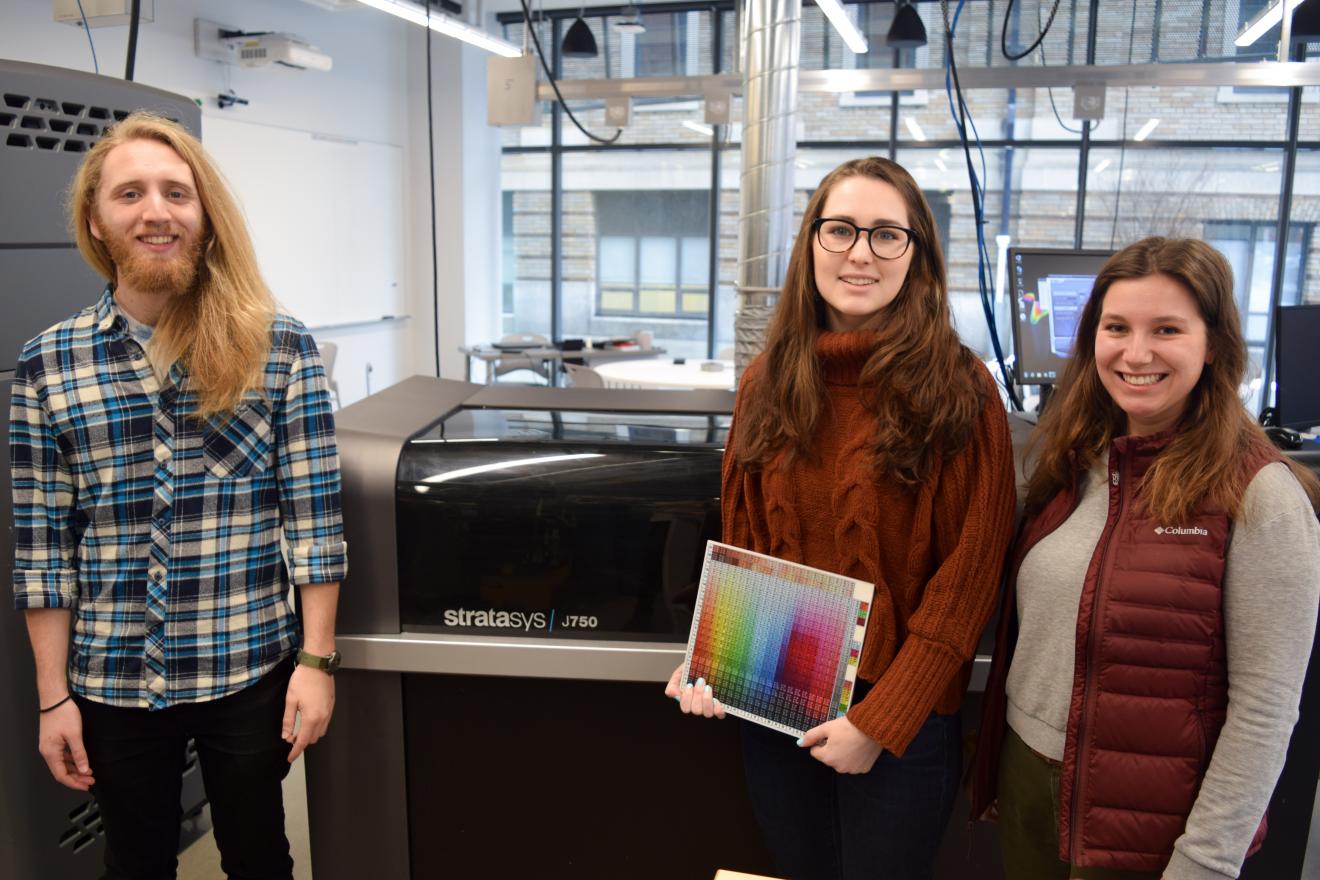
Since being awarded the grant, the team has spent the last eight months conducting mechanical inspections and electrical testing of parts they’ve created through additive manufacturing and using conductive plating. Additive manufacturing, more commonly known as 3D printing, was chosen by the group because it allows the engineer to add layers of material creating more intricate geometry than subtractive manufacturing, which removes material to create the desired object. Conductive plating, also tested by the team, allows electric current to run over a surface that would have otherwise been non-conductive material.
The team spent time working on Wentworth’s campus, which meant access to state-of-the-art additive manufacturing labs. “It was a huge advantage,” said Piscitello of the university’s resources. “I had never been at a facility with such a variety of technologies available."
The team also spent time working at Teradyne’s facilities where they utilized highly specialized equipment including 3D microscopes and Vector Network Analyzers (VNA) to inspect and measure their parts, working alongside Teradyne engineers.
“We know when we finish this project, there’s an industry that is needing this and that it is also applicable to other industries,” said Zunino. One industry is biomedical, where engineers are prototyping parts that will be used in human bodies. The need for these parts is often immediate, leaving the engineer with little time to consider all prototyping options available.
The information gathered during the team’s research will be valuable in determining the most effective prototyping process for a variety of projects.
“We are not trying to build the best wave guide, or even a new wave guide, we’re trying to figure out exactly which technologies are good at producing wave guides,” said Piscitello. Ultimately, the team aims to create a decision-making matrix for future engineers to use.
“It will help engineers decide what avenues to go down, what's worth their time, and what will help achieve the results they need,” said Peterson. The decision-making matrix will be a user-friendly, virtual tool comprised of data recorded by the students.
This team of three Wentworth students is an example of how inefficiencies encountered on co-op can translate directly to innovation. Peterson explained, “You might find something worth exploring, look for those opportunities and bring it back to your team. Start early and find openings because they’re there.”
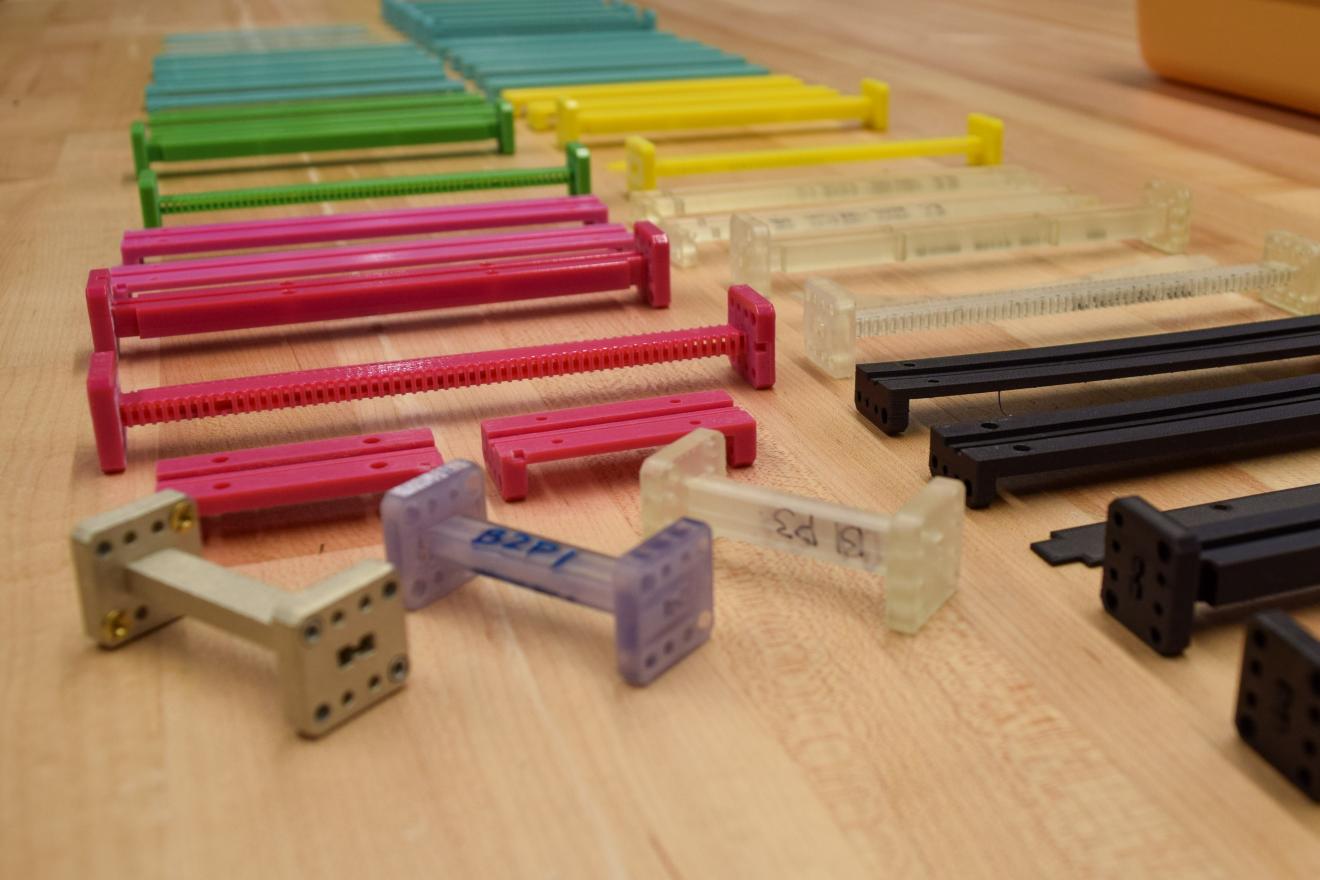
Throughout their senior design project, Peterson, Zunino and Piscitello experienced working with vendors on securing procurements, navigating timely communication, and determining how much effort is appropriate when troubleshooting a problem before moving on.
The students shared that they felt encouraged by Teradyne each step along the way. “Everyone we talked to has been excited to see us get into the industry,” said Zunino.
Upon graduation, Peterson will be joining Teradyne as a hardware engineer at their California location, Zunino will be working on drones as an electrical engineer with AeroVironment in Burlington, Mass., and Piscitello will be relocating to Kittery, Maine to join the Portsmouth Naval Shipyard to work with nuclear submarines.