Rob Trumbour, Associate Professor, Architecture
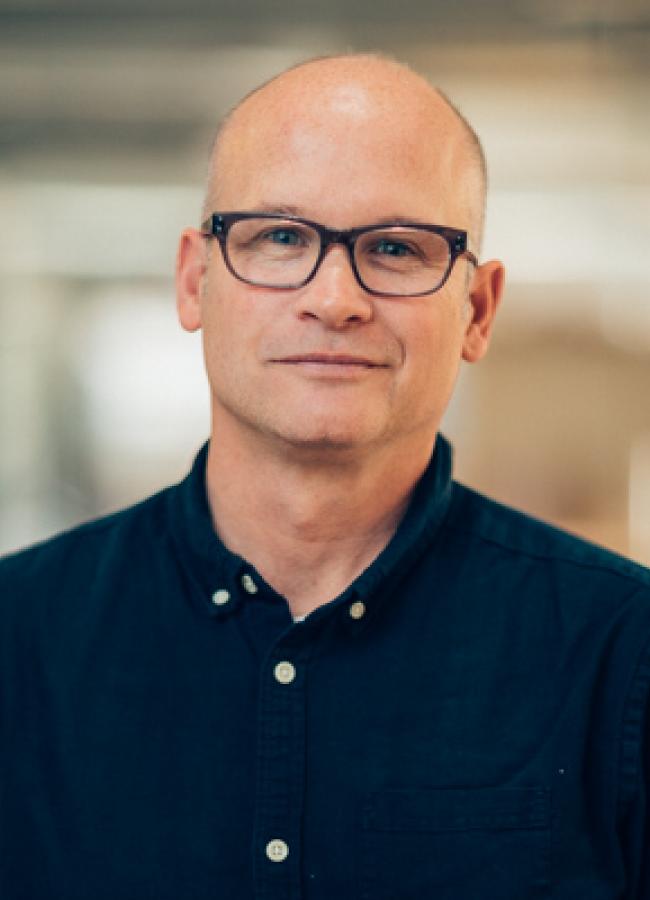
First and foremost, the William E. Roberts Professorship has given me the opportunity to offer applied research projects at a large scale, which is often unobtainable due to budget and space constraints. Architects are trained to imagine and envision at a scale that shapes the built environment we live in, but it is rare to be involved in the physical realization. The funding provided through the professorship enables me as a design instructor to build together with students, at a one to one scale with methods and materials equivalent to what is happening in the architectural, engineering and construction industries. In my courses we can go beyond standard design research by experimenting and testing innovative materials and methods of fabrication including composites and additive manufacturing. These areas of research, which are familiar in the engineering disciplines, are now becoming topics within architecture due to their capacity to address material efficiency and waste reduction, customization and industrial manufacturing methods. Over the past year my course work with students has involved material research and manufacturing methods of pre-impregnated carbon fiber as a system of building that engages in additive processes of construction. Rather than beginning with a sheet good or standardized volumetric building unit, the additive process allows you to add material where it performs best.
Additive processes have also included clay extrusion using our program’s 6 axis industrial robotic arm. In the spirit of other 3D printing processes, clay extrusion prints with a clay mixture that is customizable based on the application and is controlled through computational scripting and robotic movements. This process began with developing a custom end of arm tooling needed to perform the extrusion followed by the development of a workflow from design to production. Graduate students in an advanced fabrication seminar explored additive manufacturing methods applied directly to their yearlong thesis projects.
Lastly, work at the Autodesk Build Space in South Boston has continued to provide the program with access to amazing manufacturing tools and research support for two studio groups over the past year. The Build Space is one of three Technology Centers supported by Autodesk, and as their website states, “hosts teams from industry, academic, and startup communities doing forward-looking work in the areas of construction, manufacturing, and emerging technologies.” Work at Autodesk has included the fabrication of modular carbon fiber components and robotic foam cutting methods developed to manufacture modular precast concrete form work for complex geometries in collaboration with a leading precast manufacturing.